Malfunction Indicator Lamps
Blog Articles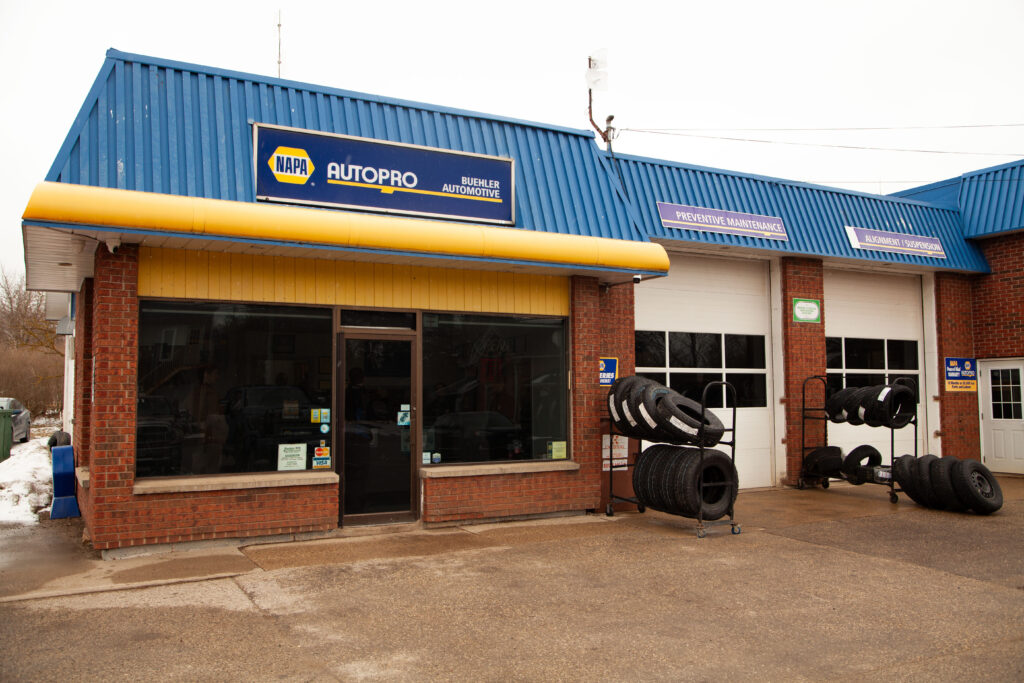
Why does that silly light keep popping up on my instrument cluster? Can I drive the vehicle with this light on? What does this symbol mean? These might be questions you’ve asked yourself in the past, and I’d like to try to provide some clarity today on what you should do when you have these questions.
If you have a Malfunction Indicator Light (MIL) illuminated on your cars instrument cluster, and you aren’t sure what it means or if it’s serious, the first thing you should do is call your trusted auto service facility. We will be more than happy to help you understand what the symbol means, and what you should be doing. Different indicators have different levels of severity, and some require you to stop driving immediately. Other indicators are less severe, and you will be perfectly ok to drive the vehicle to your repair shop. Basically if the light is amber it means make an appointment to have it looked at, but it is not urgent. If it’s red or flashing, it needs immediate attention.
So what happens when you bring your vehicle in with a malfunction light on? We will look at the light and decide what needs to be done. Some symbols may be simple and might be indicating a low tire pressure or a tail light bulb burned out. These types of issues might be a quick and simple repair and you can be on your way! Other symbols may not be so simple. If you have an engine light or ABS light on, it may take some time to look into. When this is the case we will let you know that we need to perform a diagnosis on the vehicle.
Diagnosis is the process of checking out the vehicle for a concern (in this case a malfunction light), and coming to a conclusion of what is needed to fix the concern. As vehicles become more complicated, diagnosis is becoming a common everyday practice for our technicians. In the case of an engine light being on, the initial step of the diagnosis will usually be a code scan. This will be done with a few different options of tools depending on the year, make, and model of the vehicle. Certain systems require manufacturer specific scan tools, while others can be scanned with a generic style tool. Once we are able to communicate with the vehicle computers, we are able to scan specific systems (modules) to find fault codes.
The fault codes that we find will help guide us in the right direction of where to look for the issue. After the technician retrieves the codes they might test drive the vehicle while monitoring module data to see if they can recreate the issue or find information that may help them in their process. After they have gathered the “what is happening?” information, they can begin to look into the “why is this happening?” information. The “why?” information usually involves at least 50% of the tech’s time looking at a computer screen, and the rest of their time actually looking at the car. The reason for this is because as vehicles continue to become more complicated, individual systems change and evolve. So just because the previous model year did something this way, certainly does not mean that the current model year does. The most efficient way for a technician to solve a problem is to first ensure that they fully understand the system that they are working on.
After the technician reviews wiring diagrams or system schematics, and understands where they need to go, they can proceed to testing the system wiring circuit or physical components for faults. This testing may require a variety of tools that will help them form a conclusion as to why the fault occurred, and turned on the malfunction indicator light. The testing may also require removal of vehicle components for access to the item that needs to be tested. Once they have the “why?” answer, the diagnosis is complete. Now if you approve the repairs needed, they can go about performing the repair.
This gives you a little bit of insight as to what happens in a modern day vehicle service/repair facility. The reason that diagnostics can be expensive sometimes is because of the “behind the scenes” action that is required to properly do our jobs. Factors of the billing need to include vehicle information software subscriptions, generic and manufacturer specific scan tools, scan tool updates for new model years, ongoing technician training, vehicle specific testing equipment, and simply the time it takes to access certain vehicle components for testing.
None of this information is meant to frighten you or keep you from getting your car looked at, it is simply to help you understand the process. Your service facility should have the ability to keep you informed of what the next steps are, and what those “steps” are going to cost you. We at Buehler Automotive want to help you make the best decision for what is right for you, and for your vehicle. We are more than happy to answer your call and tell you what that malfunction indicator light is trying to tell you.
Article written by Tony Martin
